Autonomous friction measurement and airport monitoring
The airport of the future will be largely autonomous and will have a high degree of remote control. This places high demands on reliable technology and monitoring, technologies that are developed in close cooperation with industry.
Autonomous vehicle control (DRIWS) is currently used at Örnsköldsvik Airport, the first airport in the world to introduce Remote Tower Control.
The project plans to continue working with the DRIWS system, including adding a third dimension, the altitude, in order to be able to report the position of flying drones to air traffic controllers through visualisation of the airport area. This visualisation is already available today but is then used for track-based vehicles.
The project will also develop the ability to perform autonomous optical friction measurement of runways. Today, mechanical friction measurement is used by pulling a wheel after a manually driven vehicle.
The optical friction measurement developed in the project is done by aiming sensors on the surface with infrared light while recording data from reflected light. The runway surface measurements will be done with sensors mounted on an electric driverless motorcycle (ATV), i.e. autonomously. The optical sensors allow a detailed classification of the conditions of the track, both in terms of friction and regarding, for example, ice and banana temperature. The optical measurement can also be done forward and over a larger surface, creating an increased ability to forecast the nature of the runway.
A self-driving quad bike is used when demo tests of the technology are carried out. Photo: Mid Sweden University.
Project idea
The trend in airports and the aviation industry in general is more autonomous, which results in lower operating costs by allowing many functions to be handled with less staff. In Sweden, many airports are operated by municipalities and regions and these are of great importance to the regional economy. This is particularly true in northern Sweden, with long distances, where trains and cars are often not time efficient alternatives.
The solution in both the short and long term is to increase cost efficiency, and safety, supported by remote control and autonomous operation and monitoring. It also means that it will be possible to operate smaller airports cost-effectively, which is very important from a regional perspective as accessibility must remain high and that the infrastructure can be used for essential functions and in case of national crises such as forest fires.
Project objectives
The overall objective of the project is an autonomous, safe and cost-effective regional airport that can serve as a model for other airports in Sweden and the rest of the world.
This is done through:
- Further developed system (DRIWS) for the monitoring and control of autonomous (electric) ground vehicles, primarily an ATV that will be used for friction measurement;
- Verified technology for autonomous optical classification of runway friction coating and measurement and visualisation of runway coating and friction with digital twin, including a demonstrator at Örnsköldsvik Airport.
- Virtual model for drone position data and conceptual model for monitoring airport functions and for the use of airport drones and for community services.
News from the project
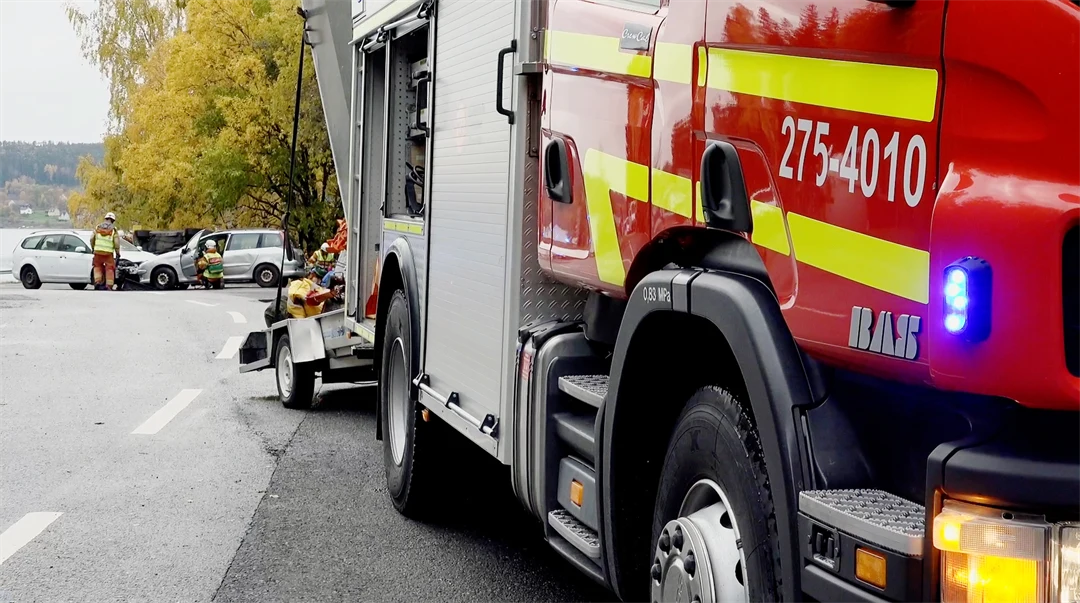
Guide drones from airports - Can save lives at a accident
Using drone technology to quickly get an overview of an accident scene provides valuable information to save time and save lives. Within the project, the airport security system DRIWS has been further developed to also include airborne objects.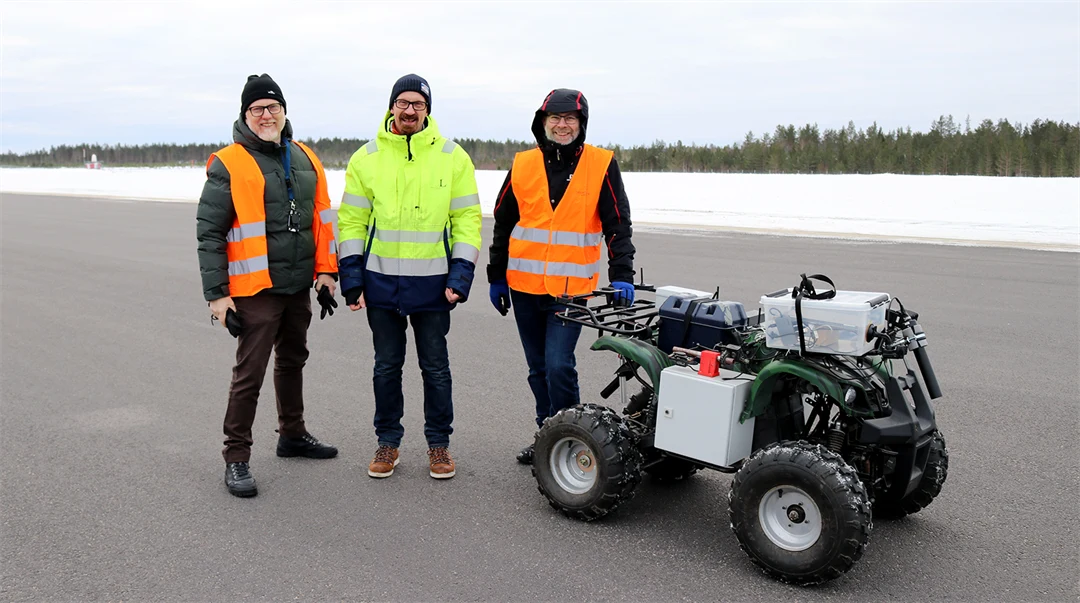
Autonomous measurement of the runway surface
A self-driving quadricycle has been developed to measure the landing surface. The measurement system combines laser and camera technology and has been further developed by the project's partner Klimator and adapted to the airport's needs.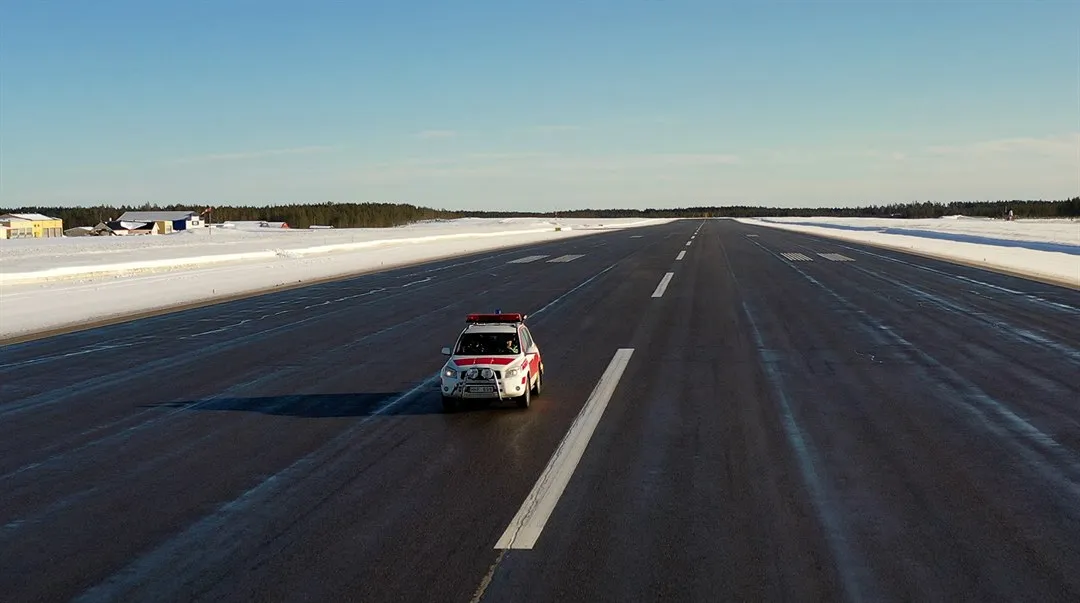
New camera technology is launched
In collaboration with the company Klimator, new technology for detecting the surface of the runway has been developed. See how the technology is tested today and how it can be used in the future!Facts
Project period
211001—240331
Partners
Research centers
Research groups
Municipal cooperation
Project leader
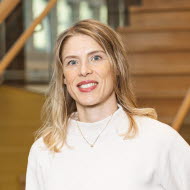
Project members
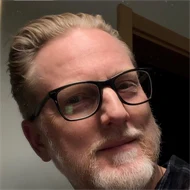