The Bioenergy gasification research group are focused on synthesis gas (“syngas”) production from biomass for automotive fuel production.
The research is directed to the thermo-chemical conversion of biomass into syngas for the downstream production of electricity, automotive fuels and chemicals, such as DME, FT fuels, ethanol, synthetic natural gas (SNG), hydrogen etc. It is so called BTL (biomass to liquids). The objective is to develop a duel fluidized bed gasifier (indirect gasifier) which can be integrated into a BTL system and further into a mechanical pulp mill with reliable technology and higher electricity/fuels/chemicals production efficiency. Thus, a gasification-based biorefinery can be realized in mechanical pulp mills.
Laboratory facility
The laboratory facility of the bioenergy research group is centralized with a pilot plant of biomass dual fluidized bed gasifier (DFBG) as shown below, which was developed by the bioenergy group. The DFBG gasifier consists of a bubbling fluidized bed steam gasifier and a circulating fluidised bed riser combustor, and has the biomass treatment capacity of 150 kWth, i.e. approx. 25 kg biomass feed per hour. The gasifier and the combustor have a height of 2.5 and 3.1 m and inner diameters (i.d.) of 300 and 90 mm, respectively. A good gas-solid contact can be realized by an in situ reformer installed above the dense bed of the fluidized bed gasifier but under the hot bed material return position. Such an in situ reformer, similar to an upper fluidized bed of olivine, is developed by the bioenergy group as shown below. Biomass is first devolatilized in the bottom fluidized bed. The volatile from biomass pyrolysis then goes through the upper part in situ reformer and experiences cracking and reforming of tars and CH4 in the hotter reformer.
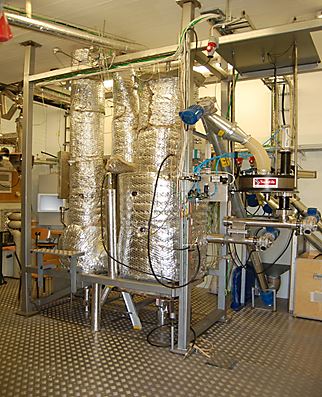